SHIELDPOLY
Our range of uniquely formulated Polyurea coatings that combine ideal properties with easy application.
What is ShieldPoly?
ShieldPoly is the branding for ShieldCrete®’s range of Polyurea’s. They are uniquely formulated Polyurea coatings that combine ideal physical properties with ease of application. They are state of the art 100% solids, flexible, spray-applied, high build, two components, fast set elastomeric coatings.
Saying you want to use a polyurea is like saying you want to use an epoxy. There are hundreds of different types and performance levels. Ensure you are using the latest and the most appropriate product to ensure you get the nicest application and the best durability for your specific case.
Our Polyurea is ideal for heavy-duty waterproofing, bund liners, abrasion resistant coatings, containment, conveyor belt repair, wastewater treatment liners, pipes, tank liners, tailings pond liners, and a host of other industrial applications. They are applicable nearly anywhere to protect the vital assets and infrastructure that keep your industry in business.
Polyurea has been used in industrial coating for over 40 years, but recent advancements in application technology and chemistry has seen the industry grow rapidly. Polyurea coatings are ideal for use on almost any surface due to their durability, flexibility, versatility, high abrasion resistance, and high chemical resistance.
Our ShieldPoly products also boast incredibly fast curing times (~15 seconds for ShieldPoly F15), even at temperatures well below O°C or in humid environments. With these exceptional properties, there’s sure to be a ShieldPoly formulation to suit your specifications. In fact, our products can even be used on conveyor belt rubber, which has been a difficult task to accomplish for the competition.
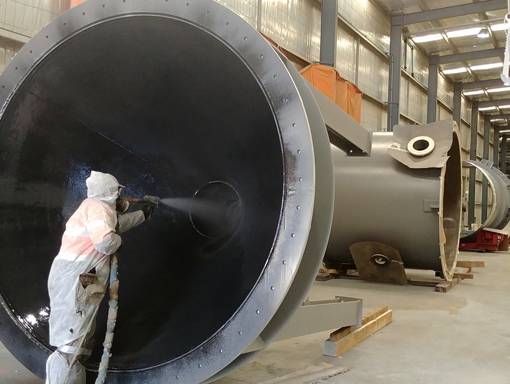
Benefits of ShieldPoly Polyurea Coatings
ShieldPoly Polyurea coatings have a range of benefits that can make it a great choice for your next application. These include:
- Return to service in 1-24hrs.
- Long recoat windows compared to others (typically 12-24hrs).
- Can be walked on in only a few minutes.
- Spans joints and cracks so you won’t need to regularly repair/re-point joint sealants.
- High chemical resistance.
- Cost competitive with epoxies and rubber lining.
- Faster job turnaround in the paint yard (no extended curing periods and no multiple coats required).
- Faster project completion and return to service than alternatives.
- No harmful VOC’s.
- Prevent hang-up and carry back of bulk materials.
- Longer lasting than EPDM liners, eliminate leaks and easier to repair if damaged.
- Seamless and can handle significant movement and traffic.
Specifications
At ShieldCrete®, we have a range of standard specifications available on request. If you want to use ShieldPoly for your next application and need a custom specification, contact us and we can write you one. When specifying Polyurea, there are key elements to consider. Not all Polyurea’s are the same. The performance is highly influenced by the combination of the following parameters (no single parameter determines performance):
- Tensile strength – High tensile strength improves puncture and tear resistance, and the higher the tensile capacity, the more resistance to particle abrasion and impacts when combined with good elongation and hardness.
- Elongation – High elongation is generally better because it allows for higher impact resistance, and resilience against thermal movement. It also helps with particle abrasion resistance when the tensile strength is still high. If bridging control joints and cracks, a bond-breaker can be specified to match the elongation capacity and the expected movement.
- Purity – Generally, the purer the polyurea the better the UV and chemical resistance. Be careful of cheap products because some people claim purity even though they have 10, 20 or even 40% urethane in the formula. Pure means no intentional hydroxyl bonds (no urethane) according to the Polyurea Development Association (PDA).
- Hardness – This isn’t hugely important for Polyurea in most situations. Abrasion resistance is better determined by the tensile and elongation balance for particle abrasion, but resistance against scraping abrasion may be improved by higher hardness.
- Taber Abrasion – This measure has been found to not correlate well with any realistic requirement for abrasion resistance of polyurea. We don’t normally pay much attention to these values but provide them for reference.
Important Note:
Unlike other Polyurea coating products, ShieldPoly does not have any propylene carbonate in the formulation. This differentiation is important because if the product gets too hot the propylene carbonate can change to propylene glycol (or polypropylene glycol) which is highly hydrophilic and can cause significant inter-coat and general blistering.
More details
The applications for our polyureas are almost endless, but they are commonly used in mining tanks and processing facilities, anywhere where high abrasion resistance is required, or where seamless waterproofing systems are required. They are used direct to substrate, over primers and over geotextiles.
Some typical uses:
- Ball & Sag Mills to replace the rubber lining
- CIL tanks and thickeners
- Floatation cells
- Secondary containment bunds
- Acid bunds
- Tailings dam liners
- Landfill liners and cap systems
- Potable water storage
- Waste water processing and storage
- Pipe linings (internal or external)
- Insulating coatings for poles and towers
- Truck tray and rail wagon lining
- Excavator buckets
- Woodchip truck liners
- Conveyor belt repairs
- Fish farm pond liners
- Encapsulation of asbestos or waterproofing old building skins
- Mining fuel tanks and truck underbodies.
Product specific details
If you would like us to design a solution and provide material quantities required for your project, please fill in the following form and we will get back to you asap:
POLYUREAS
ShieldPoly F15
Potable Water approved (AS4020) all-purpose polyurea with dielectric strength of 25kV/mm. Cost effective for a range of applications. Easier to say where it isn’t recommended:
- Conveyor Belts – ShieldPoly CV is required due to early-cure physical property requirements.
- Aggressive chemical exposure (Contact Us with exposure details).
- Extreme abrasion (use ShieldPoly AR).
- Small area to be coated (not cost effective for the full plural equipment) – use PoleKote or HA1 depending on requirements.
- On large areas if a lower cost hybrid will give the desired performance.
ShieldPoly CV
Specially formulated to match the ShieldPrime SP and ShieldPrime CV primers and to have the desired early strength, elongation and caking properties required for ultimate application to running or static conveyor belts.
ShieldPoly AR
Extra-high abrasion resistant pure polyurea for areas where the client desires even higher resistance than ShieldPoly F15. It is formulated to work equally well on conveyors or general structures like chutes and tanks.
ShieldPoly CVFR
Fire retardant version of ShieldPoly CV to solve the risk of conveyor belt fires. Can also be used to protect wood power poles from bushfires, and other general fire-resistant requirements.
HYBRIDS, URETHANES & PRIMERS
ShieldPoly TSL300
Structural – Grade polyurethane. Over 35MPa Tensile Strength, high rigidity, over 60MPa compressive strength. Designed to re-line and structurally replace or support large-scale tunnels, manholes, sewers, pipes, etc. with minimum thickness. Contact Us and we can help design this solution.
ShieldPoly HA1
Hand Applied hybrid polyurea with excellent elongation and low-cost. It has a slow cure for ease of brushing/trowelling or airless spraying. Excellent for small areas and waterproofing.
ShieldPoly PoleKote
Electrically insulating (25kV/mm Dielectric Strength) and highly corrosion and abrasion resistant hand-applied castor-based urethane designed specifically for application on power poles and streetlights at ground line. However, it has been successfully used for patch repair of polyurea also. Comes in handy blister packs and larger packs on request.
PRIMERS
ShieldPrime SP
Revolutionary 1:1, 100% solids epoxy-based primer that can be used on steel, glass, rubber and most plastics. It is also perfect for use as an intercoat primer for elastomerics like polyurea and polyurethane. 12hr plus open window (temperature and humidity dependent).
ShieldPrime UNI
100% solids primer for steel, concrete and other porous surfaces. Designed specifically for a chemical bond to polyurea. Moisture tolerant for concrete surfaces. 24hr or more open window at 25°C and 50% humidity.
Technical Documents
Available Downloads: SDS (Safety Data Sheet), TDS (Technical Data Sheet)