BELTSHIELD®
BeltShield® polyurea has been specifically developed for high abrasion, elongation, and tensile strength, such that the polyurea repair is more durable than the original belt.
What is BeltShield®?
BeltShield is the first 100% solids, complete bond system for rubber conveyor belt repair. Unlike other complicated, low flashpoint and toxic solvent-based systems, BeltShield primer and polyurea systems are designed specifically for application to running or stationary conveyer belts for minimum downtime.
BeltShield polyurea has been specifically developed for high abrasion, elongation, and tensile strength, such that the polyurea repair is more durable than the original belt, but at the same time, if the coating is damaged it won’t peel the polyurea off in massive sheets and clog up the system.
The primer we developed is a unique primer that requires no solvent to adhere to rubber and other difficult substrates. In fact, the bond with the rubber is so strong that the rubber is the weak point.
BeltShield has been used on conveyor belts for FMG, Rio Tinto and BHP.
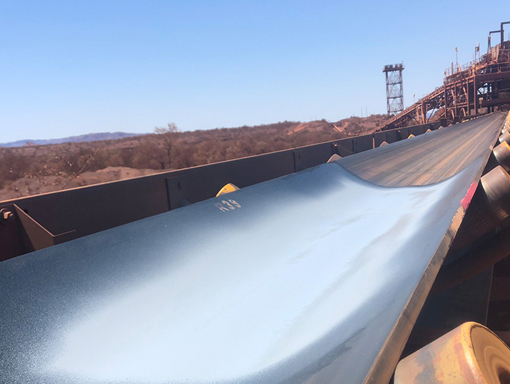
Benefits of BeltShield®?
Other cold-weld repair kits require more surface preparation than BeltShield, as well as the use of heavily solvented primers and cold-rubber products. Some others use polyurethanes that are not as durable as the belt itself, so they require constant inspection and remediation.
Alternatively, the system we have developed at BeltShield repairs the conveyor belt to a level that improves the durability of the belt, and the bond is stronger than the cohesive strength of the rubber. Our polyurea options have been developed such that the repair will last longer than the original belt.
Our solutions were originally designed to get the belt to the next shutdown (12-18 weeks) so it could be replaced. However, once it was tested, the clients realised it could be a permanent solution. We now have applications that have been running with hundreds of millions of tonnes of iron ore passing over them for more than 18 months.
If that wasn’t enough of a benefit, the BeltShield belt repair system is cost effective compared to other conventional repair options and a fraction of the cost of replacing the entire belt, even before you take into consideration the lost production downtime of alternatives.
The strength and durability of our polyurea repair products can save you replacement costs and reduce the downtime of your business. We know how frustrating it is to have your belt down for days at a time. That is why we have developed our products to have a quick turnaround time to have your conveyor belt back in operation in as little as 2 hours.
Application & Training
The application can be done by one of our trained applicators, or by site personnel, but we require them to be trained by us either way. For obvious reasons, this isn’t something you want to get wrong. Hence we provide training services on site.
The application for running belts, or large area static belt applications is done using the ShieldPrime CV and ShieldPoly CV/AR/FR system (depending on application requirements). Hence, you need to have a full polyurea application setup. We can assist with this if required.
The hand applied systems are for small area repairs and can be applied with a brush, roller or airless spray (in most cases). The training requirements are less stringent, but it is still recommended to ensure the products are used correctly and you get maximum benefit from the product.
Availability
The products have varying availability by region, please contact your local office to enquire about availability.
Point of Contact
Tad Bass
CEO & Technical Director
Ph +66 (0)92 863 9833
Email: [email protected]
Technical Documents
Available Downloads: SDS (Safety Data Sheet), TDS (Technical Data Sheet)
FEATURED CASE STUDY
Sag Mill Polyurea Reline
The operators of the gold mine wanted a way to protect their assets from the high levels of corrosion that can be found on site. This project profile covers the Sag Mill re-lining.
ShieldPoly F-15 was selected due to its superior physical properties, technical support, and proven performance. In this case ShieldCrete International managed the project along with our sub-contractors. The ShieldPoly was applied underneath the wear plates to a thickness of 6mm on the internal walls of the mills to prevent the issue of corrosion that commonly occurs with the rubber lining alternatives, particularly at the rubber seams.
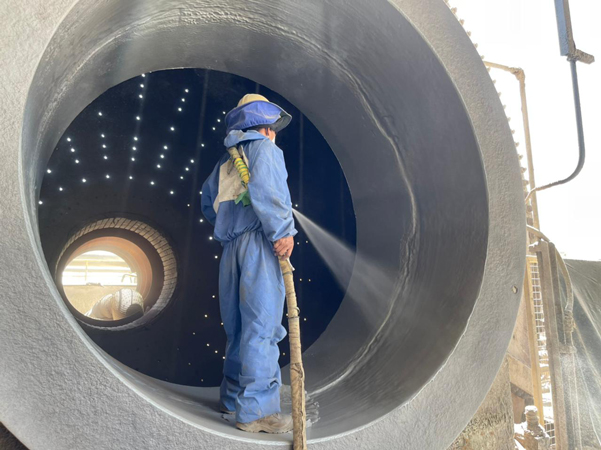